Wooden fences develop holes from slow weathering or impact damage, but these are easy to repair with wood filler and paint. Staining and sealing also prolong the life of your R.C Fence LLC.
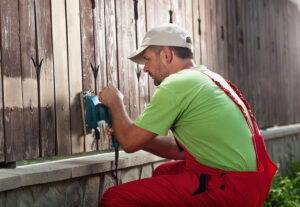
Ask your neighbors if you can access their side of the fence during the repair. This makes the job easier and faster.
A damaged fence post is a common problem that many homeowners face at some point. Usually, it’s due to severe weather conditions like heavy winds that can cause the soil to erode and lead to instability of the posts or wood rot caused by excessive moisture sitting against the post. It can also be due to poor materials used for construction of the fence or casual neglect such as failing to inspect the fence regularly for signs of damage and deterioration.
The best way to fix a damaged fence post is to replace it. However, before replacing it it’s important to evaluate the damage and determine if it makes more sense to repair the existing post instead of replacing it. This is especially true if the existing fence is quite old and showing signs of deterioration or damage.
Generally, if the damage is acute, like being struck by a vehicle or a bad storm, it may make more sense to repair it rather than replace it completely. On the other hand, if it’s chronic and likely to get worse unless addressed, such as wood rot, it may be better to replace it entirely.
Before starting the repair process, it’s a good idea to walk around the entire fence and examine the condition of each post. Be sure to look for cracks and chips in the boards as well as any areas where the fence wobbles or if there are signs of insect infestation like termite holes or trails.
It’s also worth noting if any posts are leaning. If left unattended, this could cause the rest of the fence to eventually fall down or break. It’s also important to check the ground around each post for looseness or if it has been shifted or buried in dirt that is too deep.
Once you’ve assessed the damage, it’s time to gather your tools and materials for the repair job. This should include a hammer, nails/screws, drill with proper bit sizes, saw, wood glue or epoxy, replacement boards/posts/pickets, level tool and wood stain/sealer/protector. It’s always a good idea to wear protective gear, including goggles and gloves.
Broken Rails
The rails that run from post to post across the top and bottom of your wooden fence are critical for its structure. They hold the fence boards and help to keep them in place, so if you notice any damage to these parts of your wooden fencing system, it is important to fix them right away.
While rot is the most common cause of broken rails, impacts can also break them. The best way to prevent this type of damage is by regularly applying wood preservative to the area, which can be purchased at most home improvement stores.
Another way to reduce the risk of broken rails is by increasing inspection frequency and using the most sophisticated testing methods available. This gives railroad companies a better chance of catching cracks before they become major safety hazards. However, this can increase the cost of running a train, so it is important to balance safety and efficiency when making these decisions.
As a result of these technological advances, the number of train derailments has dropped in recent decades. But broken rails remain the leading cause of derailments on mainline tracks, with a great potential for injury and even loss of life.
When a rail breaks, it can cause the wheels of a train to shift off track, causing the train to become unbalanced and possibly derailing. A train derailment can also have catastrophic consequences for the people on and around the trains, as well as the environment. For this reason, railroads are under constant pressure to improve the quality of their rail tracks and to reduce the number of broken rails they have to deal with.
Leaning Posts
Leaning fence posts can be difficult to fix, especially if the post is breaking at the base or has rotted. This can leave the entire stretch of fence in danger of collapse, and it’s important to get to the bottom of the problem and find a long-term solution.
Depending on the cause of the lean, your options may include strengthening the concrete footing, weatherproofing the fence, or changing to a different type of fencing. If the posts are simply unseated or weakened from external forces, however, you can usually straighten them with a few simple steps.
First, step back and examine the extent of the lean. Note its degree and direction, then use a spirit level to ensure the post is level. This will help you decide whether it’s an isolated issue or a symptom of a bigger problem.
If the post is merely unseated, dig around it with a shovel until you hit the concrete base holding it up. This will give you a better idea of how much support the post has and what needs to be done to it to keep it stable.
When digging, try not to remove too much of the concrete from the hole. You may need to re-use it later in the process. Once you’re confident the base of the post is solid, you can dig further to expose a broken or rotting section of the post. If the break is above ground, you’ll need to install a post mender.
Post menders (also known as spikes or anchors) are metal devices designed to be driven into the ground and fastened to a leaning fence post to stabilize it. They’re often used to repair wood fence posts, but they can also be installed on metal ones.
Screw one of these metal anchors to the top of a weak fence post and drive another into the ground below it, using a sledgehammer or other heavy tool. This will help to strengthen the connection between the broken post and its concrete anchor. If the damage to the post is serious, you’ll need to replace it entirely.
Falling Panels
If you find a panel that has fallen off your fence, it’s important to check the rest of the structure. If the rest of the panels are intact, the easiest fix is to re-glue the panel to its frame using Titebond III wood glue. If the frames are exposed, stain the area to match the surrounding wood tone. You can also paint larger areas with acrylics, thinned down with water. You can then blend colors to match the tone and make the repair nearly invisible.
The failure of the panel could have been caused by a number of issues. It appears that the slotted holes for fixings were too close to the edge of the panel, and the sheeting was quite thin. This may have caused material overload if the panel had been subjected to dynamic effects.